

- #MACH4 CNC CONTROLLER ARMV8 MANUAL#
- #MACH4 CNC CONTROLLER ARMV8 SOFTWARE#
- #MACH4 CNC CONTROLLER ARMV8 PC#
All I/O terminals are clearly marked for quick and easy installation. Each board has 16 input terminals and 8 output terminals. In order to use encoders for Axis Feedback purpose, 'Closed Loop Activaion' must be purchased.ħ535 Board : The I/O Termination board ( 7535P or 7535N) provides 24 Volts optically isolated digital I/O. When used with Drive Interface Board (EPx-DIB) for Maxsine AC Servo Drives, this board provides almost plug and play installation. Using the 7737 Board greatly simplifies wiring for Encoder Feedback and Step/Dir channels on J7 and J8.ħ737 Board : The pn7737 Differential Step/Direction and Encoder Board allows access to the Step/Direction and Encoder channels on J7 and J8 plugs, and allows a simple plug-and-play setup using standard RJ45/Ethernet cables.
#MACH4 CNC CONTROLLER ARMV8 SOFTWARE#
INTG-CLOOP : This software feature allows Closed-Loop operation and enables Step/Dir channels 0-3 and Encoder channels 3-6 on J8, as well as Step/Dir channels 4-5 and Encoder channels 7-8 on J7. For packages and more information visit ARCPRO page. 77ISO is required to read the plasma analog voltage. HiCON-ADC : This software feature allows the use of the 2 analog inputs located on J6.ĪrcPro Plasma features : M4ARCPRO software feature allows the use of ArcPro Plasma screen. This feature also enables Mach4 Sync Outputs (M62/M63). Useful if the built-in inputs and outputs are not sufficient. HiCON-EXTIO : This software feature extends the number of available I/O by enabling ports J7 and J8.
#MACH4 CNC CONTROLLER ARMV8 PC#
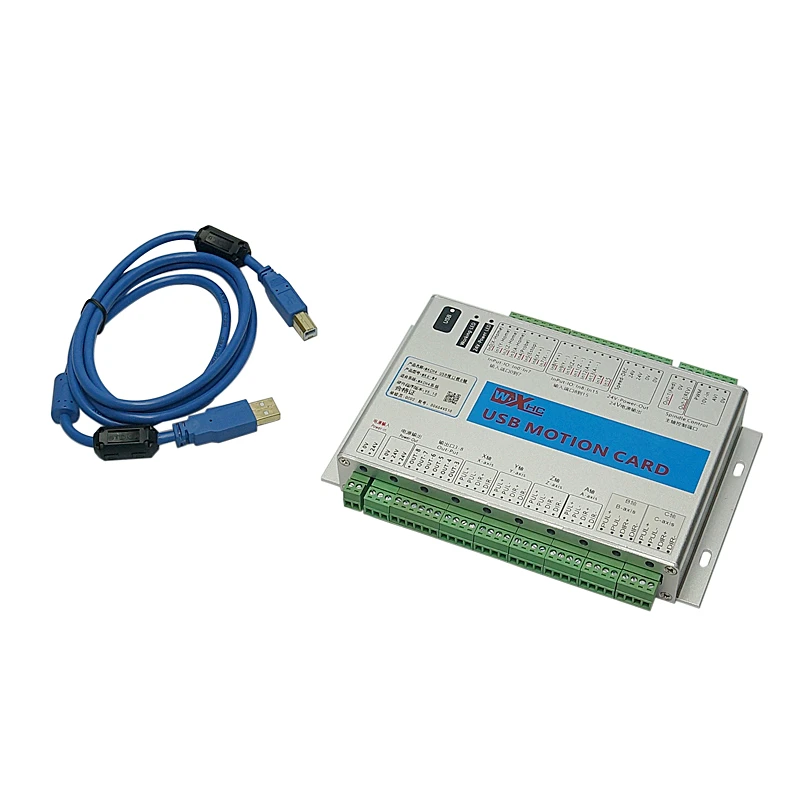
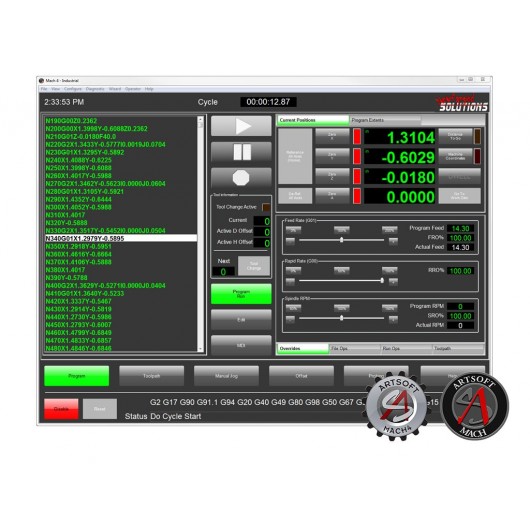
We offer, thus making the installation almost plug-and-play With 7737 board, you can use RJ45 cables between the controller and the motor drivers.
#MACH4 CNC CONTROLLER ARMV8 MANUAL#
In addition, the DROs on Mach4 will show the actual machine position instead of just a step counter.Ĭlosed loop option also allows you to use the mill in manual mode where you manipulate the axis manually while seeing the actual positions in the DROs. This preventsįollowing errors from accumulating. Missing steps during transmission, and will automatically apply the necessary position correction at the start of the next move. This setup provides a great solution for applications that require accuracy and reliability.
